Assessing Maintenance Costs at Hyundai Factories

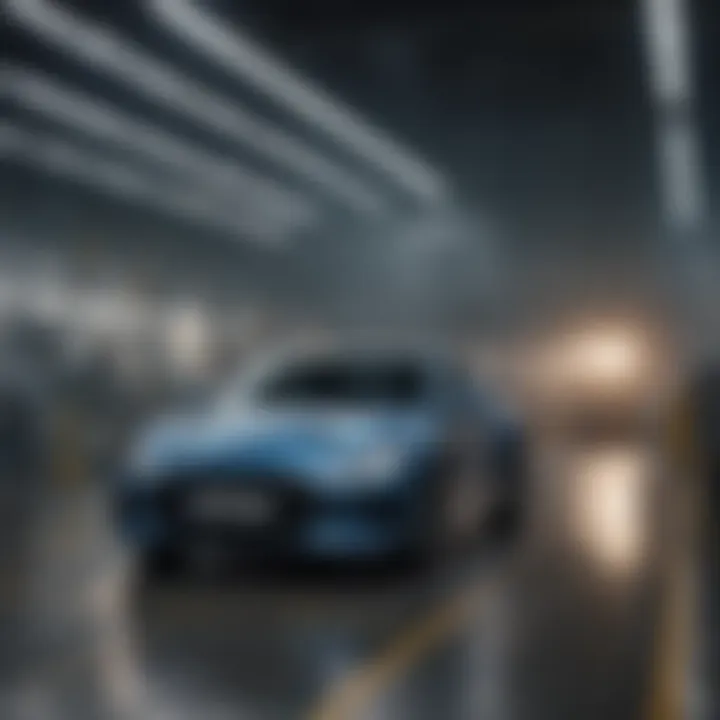
Intro
Understanding the intricacies of maintenance costs in factories is critical in today's competitive automotive landscape. When it comes to Hyundai, a company that has burgeoned into a globally recognized automotive manufacturer, these costs play a pivotal role in determining the effectiveness of its operations. As we dig deeper into the realm of Hyundai's factory maintenance expenses, it’s essential to examine how various factors influence these costs and subsequently the overall production efficiency.
The automotive industry is in a constant state of flux, influenced by advancements in technology, shifts in consumer preferences, and the rising importance of sustainability. Maintenance strategies are not just necessary expenses; they can significantly enhance profitability and operational efficacy.
This piece aims to elucidate multiple facets of Hyundai's factory maintenance costs: - the factors that dictate these expenses - the diverse maintenance strategies employed in its manufacturing processes - implications of these costs on the broader automotive industry. By scrutinizing preventive maintenance efforts and the integration of advanced technology, we can glean valuable insights pertinent to industry enthusiasts and professionals alike.
Preface to Hyundai Manufacturing
Diving into the world of Hyundai manufacturing isn't just about understanding their cars; it's about grasping the intricate dynamics of how these machines come to life. The maintenance of Hyundai factories plays a critical role in maintaining the production lines that yield vehicles so beloved by consumers. This aspect of manufacturing is not often the center of attention, yet it holds vast implications for cost efficiency and operational longevity.
In this section, we will explore the historical underpinnings of Hyundai factories and how they’ve adapted over time. Furthermore, we'll take a closer look at today's global manufacturing landscape, where competition is fierce, and innovation is paramount. Understanding these elements is vital as they affect the overall maintenance costs, influencing strategies that keep the factories running smoothly without breaking the bank.
The Importance of Introduction to Hyundai Manufacturing
Focusing on Hyundai's manufacturing process reveals key insights about its operational strategies. By examining the root of its success and the hurdles it faces, one can appreciate why maintenance costs are not simply an overhead but a strategic area that can bolster or hinder performance. Hyundai's commitment to quality and efficiency is deeply intertwined with how they handle maintenance, which ultimately affects every car that rolls off the assembly line.
Historical Background of Hyundai Factories
Hyundai, a name synonymous with automotive resilience, was born in 1967. Initially, it started as a construction firm but soon diversified into manufacturing vehicles. The establishment of the Ulsan plant in 1968 marked a turning point, as it became one of the largest automotive manufacturing facilities worldwide. During the late 20th century, Hyundai faced numerous challenges, including economic recessions and fierce global competition. However, instead of folding under pressure, they pivoted towards innovation and quality, evolving their factories to incorporate more automated processes. This historical backdrop lays the foundation for understanding current maintenance practices and how they manage costs associated with keeping machinery and equipment in prime condition.
Current Global Manufacturing Landscape
Today, the global manufacturing landscape is a complex web of competition and technological advancement. Hyundai operates within this landscape, facing challenges from rival companies like Toyota and Ford. The integration of smart technologies and data analytics into manufacturing has become a pivotal element. Companies are increasingly investing in automated maintenance solutions to minimize downtime and maximize productivity.
"In the realm of automotive manufacturing, efficiency isn't just a goal; it's a necessity for survival."
The rising cost of labor, coupled with the necessity to remain compliant with environmental regulations, pressures manufacturers to carefully manage their maintenance expenses. From using advanced software for predictive maintenance to adopting agile workforces, Hyundai has positioned itself to not only survive but thrive in this dynamic marketplace. Understanding these aspects will provide vital context as we delve deeper into the specifics of maintenance costs in subsequent sections.
Understanding Maintenance Costs
Understanding maintenance costs is pivotal not just for Hyundai, but for anyone vested in the mechanics of factory operations. These costs often represent a considerable chunk of the overall budget for manufacturers. Grasping the nuances of maintenance expenditures helps organizations like Hyundai make informed decisions regarding their operational strategies, investment allocations, and overall production efficiency.
Reflecting on the crux of the matter, maintenance costs can impact everything from the day-to-day productivity of the factory to long-term strategic goals. When factories experience unexpected downtimes due to maintenance issues, production halts, and a ripple effect occurs across supply chains. So, analyzing these costs can empower Hyundai to optimize its operations, ensuring that every dollar spent contributes to enhancing the efficiency and sustainability of manufacturing processes.
Definition of Maintenance Costs
In simple terms, maintenance costs refer to the expenses incurred to keep equipment and facilities in working condition. These costs span a range of activities, from routine inspections to major repairs. Unlike some other production expenses, maintenance expenditures can be unpredictable and vary significantly depending on numerous factors, including the age of the equipment and the complexity of machinery involved.
To break it down:
- Routine Maintenance includes regular checks and services to prevent breakdowns.
- Corrective Maintenance involves fixing issues once they’ve occurred, often resulting in more significant costs due to unplanned halts.
- Emergency Repairs can be the most costly, arising unexpectedly, disrupting operations and often incurring premium rates for urgent services.
"Understanding the fine print of maintenance costs often separates successful manufacturers from their less-adaptable peers."
As maintenance can significantly affect the productivity of factories, companies like Hyundai must ensure they have a robust definition and comprehensive understanding of what these costs entail.
Components of Maintenance Expenses
Diving deeper, maintenance expenses can be dissected into several essential components that help in analyzing costs effectively:
- Labor Costs: Wages paid to technicians and maintenance staff is a major part of any maintenance budget. It's essential to have well-trained personnel to execute maintenance tasks efficiently.
- Parts and Materials: Replacement components and consumables required for repairs or maintenance activities also constitute a noticeable fraction of the budget. Over time, specific machinery may require more frequent parts replacement.
- Tools and Equipment: The necessary tools for maintenance tasks, whether for monitoring equipment efficiency or conducting repairs, add to the expenses. Investing in quality tools can yield long-term savings.
- Downtime Costs: Each hour a machine is offline can be a loss in productivity and revenue. This is sometimes the most challenging component to quantify but undeniably affects the bottom line.
- Contracted Services: Sometimes, it’s more cost-effective to outsource certain maintenance tasks instead of handling everything in-house. Having a third-party service can sometimes streamline and reduce costs.
- Training: As technology evolves, workforce training becomes an unavoidable expense to keep skills sharp and in line with advanced manufacturing practices.
Acknowledging and efficiently managing these components will not just help Hyundai understand their current maintenance load but also strategize future efforts to mitigate costs and improve overall productivity.
Factors Influencing Maintenance Costs
In understanding the financial health of Hyundai's manufacturing operations, the factors influencing maintenance costs stand out as crucial elements. By delving into these aspects, one can appreciate not only how costs accumulate but also how they can be managed and optimized. Maintenance costs don't occur in a vacuum; they are influenced by many moving parts within the factory ecosystem. Addressing these factors can lead to more efficient operations and ultimately, higher profitability.
Age of Equipment
The age of equipment has a notable impact on maintenance expenses. Older machinery often requires more frequent repairs and may not operate as efficiently as newer models. As equipment ages, parts can become worn out, leading to more significant chances of breakdowns. For example, a 15-year-old stamping machine is likely to demand more diligent upkeep than its 5-year-old counterpart. The costs pile up, not only due to repairs but also because older machines may consume more energy, thus raising utility bills.
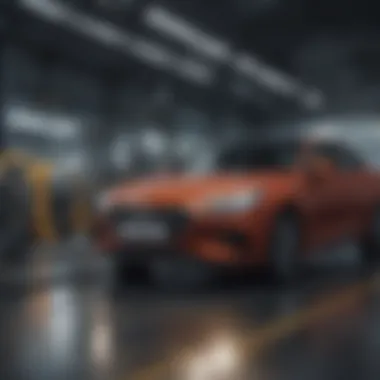
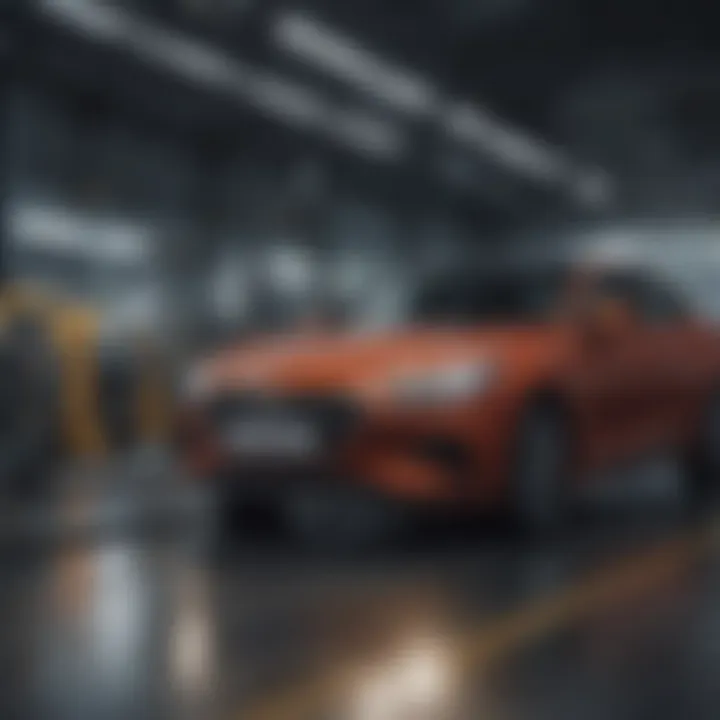
Moreover, the costs of parts for older equipment can add another layer of financial strain. If components are no longer manufactured, facilities may need to seek second-hand parts, leading to increased costs and extended downtime during repairs. In this sense, carefully evaluating the life cycle of equipment can serve as a foundational strategy for managing costs effectively. Regularly replacing or upgrading equipment can mitigate prolonged maintenance expenses and keep operations running smoothly.
Type of Operations
The nature of operations within a Hyundai factory also plays a significant role in determining maintenance costs. Factories that engage in complex operations, such as producing high-tech components, may face different challenges compared to those focused on simpler tasks. More intricate processes often require specialized machinery, which can escalate maintenance costs. For instance, if a factory is engaged in high-precision manufacturing, it may need to invest in more robust maintenance contracts to ensure machinery is operating at peak performance.
Furthermore, diverse manufacturing practices across different facilities can lead to fluctuations in maintenance expenses. Facilities operating on a just-in-time (JIT) production model might prioritize more flexible, frequent maintenance checks to adapt to changing demands. On the flip side, traditional, volume-driven approaches might lean towards scheduled maintenance. Understanding the intricacies of these operational types can aid in tailoring maintenance strategies that suit the specific environment and mitigate costs accordingly.
Labor Costs and Workforce Efficiency
Labor costs remain a significant factor when assessing maintenance expenditures. The proficiency and efficiency of the workforce directly relate to how well a factory maintains its equipment. A well-trained maintenance team can fix issues quickly and prevent minor problems from snowballing into costly repairs. In scenarios where the labor force is inexperienced or lacks proper training, it could result in higher expenses due to inefficiency.
Moreover, labor costs are not solely about hourly wages. The broader context includes training expenses, turnover rates, and the intrinsic value of efficiency. According to industry statistics, investing in workforce development can yield returns that far exceed the initial outlay. An efficient workforce can decrease downtime, enhance production quality, and ultimately drive down maintenance costs in the long run.
"A skilled workforce is an investment, not just a cost. Their efficiency can dramatically alter not only the maintenance landscape but also the factory's overall performance."
In sum, understanding these three critical factors—equipment age, operational type, and labor efficiency—provides a nuanced view of maintenance costs in Hyundai’s manufacturing process. Each element interlaces with the others, forming a complex web of influence on overall fiscal health.
Maintenance Strategies in Hyundai Factories
When we think about the performance of a manufacturing entity like Hyundai, it's vital to focus on how it approaches its maintenance strategies. The way a factory maintains its equipment can significantly impact production efficiency, safety, and long-term viability. In an industry where precision and speed can make or break a business, having solid maintenance strategies is akin to laying down the foundation of a sturdy house; if the base isn't strong, everything built on it is at risk.
In Hyundai's case, implementing effective maintenance strategies can lead to reduced downtime, optimized resource allocation, and consequently, improved cost efficiency. Organizations must keep a keen eye on how maintenance costs can eat into profit margins and overall operational performance.
These strategies can generally be classified into preventive and corrective maintenance approaches. Each brings its set of advantages, forms an integral part of Hyundai's operation, and reflects in its financials.
Preventive Maintenance Approaches
Preventive maintenance is primarily about foresight. It aims to anticipate problems before they escalate into serious issues. This approach is like a seasoned traveler who checks their vehicle regularly, ensuring oil levels are topped and tires are adequately inflated, rather than waiting for the engine to start knocking or a tire to burst before taking action.
At Hyundai, preventive maintenance begins with routine inspections, regular service intervals, and adherence to manufacturer guidelines. These activities are instrumental in maintaining equipment health and operational efficiency. The following elements highlight the importance of preventive maintenance:
- Cost Savings: By addressing potential breakdowns before they happen, costs associated with repairs and production stoppages can be significantly minimized.
- Increased Equipment Lifespan: Regular maintenance extends the life of machinery and equipment, allowing Hyundai to make the most out of its investments.
- Improved Safety: Factories are inherently hazardous environments. A well-maintained machine is less likely to malfunction, which reduces workplace accidents.
One must also consider the role of training in implementing preventive maintenance strategies. Workers should be thoroughly trained in recognizing early signs of wear and tear. Their observations can serve as a first line of defense against unexpected failures. This sense of ownership can transform a group of employees into vigilant guardians of the factory’s operational integrity.
Corrective Maintenance Practices
While preventive maintenance aims for forethought, corrective maintenance is all about action in response to issues that have already emerged. This type of strategy can be thought of as a firefighter rushing to put out a blaze after it ignites. Not always ideal but necessary when unforeseen circumstances arise.
At Hyundai, corrective maintenance involves rapidly addressing equipment failures and breakdowns. Responding efficiently to these challenges is essential to minimizing downtime, which is often the Achilles' heel for manufacturers. Here are some aspects to consider:
- Rapid Response Teams: Factories often have dedicated teams in place for urgent corrective actions. Their training ensures they can quickly diagnose problems, facilitating prompt repairs.
- Root Cause Analysis: After a failure, it's essential to investigate and identify why it occurred. This ensures that if the issue arises again, corrective measures can be preemptively put in place.
- Data Tracking: Leveraging technology can create a transparent feedback loop. By documenting incidents, Hyundai can spot patterns in failures and develop strategies to mitigate those in the future.
It’s important to note that while corrective maintenance is essential, relying on it as a primary strategy can be financially draining over time. The essence of a robust maintenance strategy lies in the balance between preventive and corrective actions. Each has its role in the grand performance of Hyundai’s factory operations and can lead to a more stable and efficient production environment.
"An ounce of prevention is worth a pound of cure."
This old adage rings particularly true in the realm of factory maintenance. To ensure a sustainable future, Hyundai must strive for a seamless blend of both preventative and corrective practices that not only uphold but enhance production standards.
Role of Technology in Maintenance
In today’s manufacturing landscape, technology plays a pivotal role in shaping maintenance strategies, especially in settings like Hyundai factories. The integration of advanced technologies not only streamlines operations but also significantly reduces maintenance costs. By leveraging innovative tools and methodologies, Hyundai can enhance the reliability of its equipment and improve the overall efficiency of its operations.
Automation and Robotics
The adoption of automation and robotics in Hyundai’s manufacturing facilities is akin to adding a turbocharger to an already powerful engine. It boosts productivity by allowing machines to perform tasks with precision, speed, and consistency. Automation reduces human error, which is often a significant contributor to breakdowns and maintenance costs.
Consider, for instance, Hyundai’s use of robotic arms in assembly lines. These robots, programmed with intricate algorithms, can handle components that are heavy or require exacting detail in placement, something that may strain human operators. As a result, there’s less wear-and-tear on the equipment, translating into lower maintenance needs. An important aspect of automation is the ability to seamlessly integrate with existing systems, allowing for better tracking of equipment usage and maintenance schedules.
Furthermore, these automated systems often come with their own diagnostic tools, enabling predictive maintenance. This means that rather than waiting for a component to fail, the technology can alert operators to potential issues before they become major problems. In a way, it’s like having a crystal ball that provides insights into the longevity of your machines, helping to avoid costly downtime.
Data Analytics for Predictive Maintenance
The use of data analytics for predictive maintenance is not just a trend; it’s quickly becoming a necessity for manufacturers looking to stay competitive. By collecting data from various machinery and processes, Hyundai can analyze this information to predict when maintenance should occur.

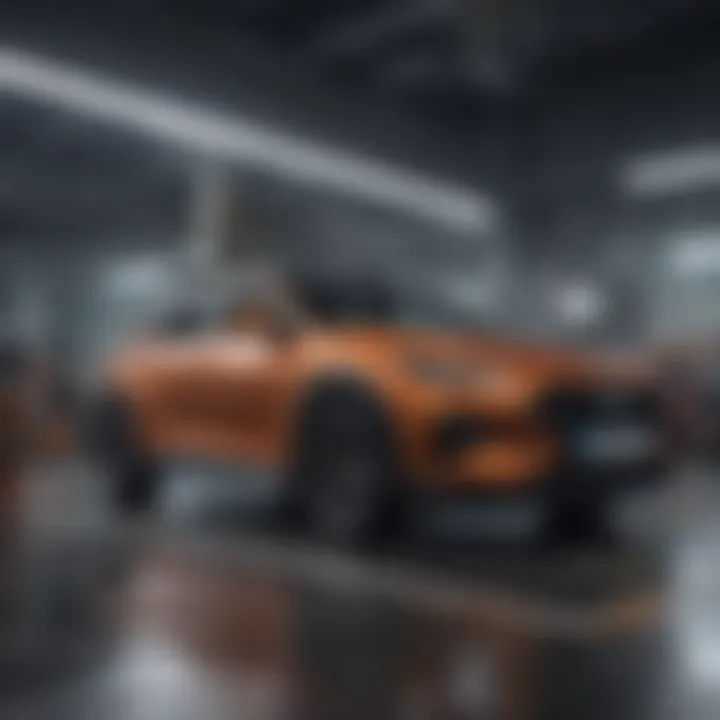
This predictive approach can vastly improve workflow and minimize disruptions. For example, if sensors installed on machinery detect unusual vibrations or fluctuations in temperature, they can relay this data back to the central system. Hyundai can then schedule maintenance during non-peak hours, which minimizes impact on production schedules.
- Key Benefits of Data Analytics:
- Reduced Unexpected Failures: Predictive maintenance allows Hyundai to avoid sudden breakdowns, which can cost not only in terms of repairs but also in lost production.
- Optimized Resource Allocation: By understanding when maintenance is likely to be needed, resources and manpower can be allocated more efficiently.
- Improved Safety: With better monitoring, the likelihood of accidents caused by equipment failure minimizes.
"Implementing data-driven insights in maintenance not only saves money but also enhances the safety and productivity of a factory environment."
Economic Implications of Maintenance Costs
Understanding the economic impact of maintenance costs in Hyundai factories is pivotal for grasping how these expenses influence the company's bottom line. It's not just about keeping machinery running; it's about optimizing operational expenditures to enhance profitability. A well-maintained factory can lead to smoother production cycles, reduced downtime, and ultimately, better product quality.
When calculating these costs, several specific elements need to be considered. The first is the direct correlation between maintenance and production efficiency. Inefficient maintenance strategies can lead to a lag in the production line, which translates directly to lost revenue. Hence, focusing on effective maintenance results in smoother operations.
Impact on Production Efficiency
Production efficiency is the lifeblood of any manufacturing operation, including Hyundai factories. When machines run at peak performance, production levels can remain high, and consequently, profit margins can expand. Unplanned maintenance, on the other hand, can be a wrench in the works. Here are some critical points illustrating how maintenance impacts production efficiency:
- Reduced Downtime: Regular maintenance schedules ensure that equipment operates without sudden breakdowns, which can halt production.
- Consistency in Output: Well-maintained machinery usually has fewer fluctuations in productivity, meaning that Hyundai can consistently meet the demands of the market.
- Quality Control: Machinery that is kept in good shape produces higher-quality products, which can enhance customer satisfaction.
The reality is that when machines break down unexpectedly, not only is there the immediate cost of repairs, but the ripple effects can impact supplier relationships and inventory management as well. Therefore, investing in a robust maintenance program is not just a good practice; it’s crucial for long-term success.
Budget Allocation for Maintenance
Getting the budget allocation right for maintenance costs is a balancing act. Hyundai needs to invest enough resources to keep its machinery in optimal condition without breaking the bank. A few considerations come into play here:
- Percentage of Total Budget: Typically, the maintenance budget is set as a percentage of overall operational costs. Keeping a close eye on historical data can help set realistic expectations.
- Forecasting Future Costs: Anticipating future maintenance expenses is essential. This includes accounting for possible equipment upgrades or replacements that may be on the horizon.
- Allocation for Innovation: As technology advances, new maintenance methodologies such as predictive maintenance tools may call for initial higher investments but can lead to long-term savings.
Allocating the correct budget is vital for ensuring that the factories can operate without interruption. An effectively planned budget doesn't just cover the routine expenses but allows for innovations that can lead to enhanced efficiency and reduced costs down the line.
Challenges Faced in Maintenance Management
Maintaining the equipment and machinery in Hyundai factories is not just a necessity; it’s a strategic imperative. Effective maintenance management directly impacts production efficiency, quality, and ultimately, profitability. However, it comes with its own set of challenges that need careful navigation.
Assessing Equipment Life Cycles
One major challenge arises in the assessment of equipment life cycles. Each machine has a finite lifespan, which can be influenced by various factors such as usage intensity, maintenance frequency, and environmental conditions. If Hyundai factories misjudge the remaining life of critical equipment, they could face unexpected failures that disrupt production.
Evaluating the life cycle involves going beyond basic statistics. It requires an integrated understanding of how equipment performs over time. Regular monitoring and analysis can help in identifying patterns regarding wear and tear. This is where technology starts playing a significant role. By employing data analytics and tracking usage history, maintenance teams can formulate a more accurate picture of when a machine is approaching its end.
- Regular inspections should be scheduled to assess machinery conditions so that data gathered can inform operational decisions.
- Predictive maintenance models can be developed using machine learning algorithms, projecting potential failure points before they become severe issues.
Understanding these factors can help mitigate risks, ensuring constant production flow and minimizing costs related to machine replacements or repairs.
Managing Unexpected Downtime
Shifting gears, we encounter another substantial challenge: managing unexpected downtime. This refers to unplanned interruptions in production due to equipment failures or other unforeseen circumstances. Such downtime can be costly, not just in the direct monetary sense but also in terms of lost productivity and diminished customer satisfaction.
Sometimes, the root causes for unexpected downtime can be elusive. It's essential for Hyundai's maintenance teams to maintain a thorough and ongoing dialogue concerning operational efficiency and equipment robustness.
To tackle this issue, companies are increasingly adopting preventive strategies:
- Detailed maintenance logs: Keeping meticulous records of maintenance activities allowing for better trend analysis that can help predict future failures.
- Employee training: Ensuring that all staff involved are educated in proper operational protocols can significantly reduce mishaps.
- Contingency plans: Establishing contingency frameworks for quick actions in case of unpredicted downtimes helps mitigate impact.
"A stitch in time saves nine" is an apt proverb to consider when it comes to addressing potential equipment issues early on before they escalate into major problems.
Ultimately, while challenges in maintenance management persist, addressing them with a strategic approach can not only save costs but also support Hyundai's commitment to optimal operational efficiency.
Comparative Analysis with Other Manufacturers
In the realm of automotive manufacturing, understanding maintenance costs is not just a solitary exercise; it's paramount to benchmark against the competition. For Hyundai, conducting a comparative analysis with other manufacturers serves as a valuable tool to gain insights into cost management strategies, operational efficiency, and overall industry trends. By examining how Hyundai's maintenance expenses stack up against those of its peers, we can identify areas for improvement and establish best practices that drive innovation.
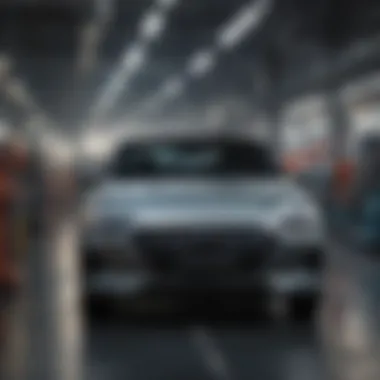
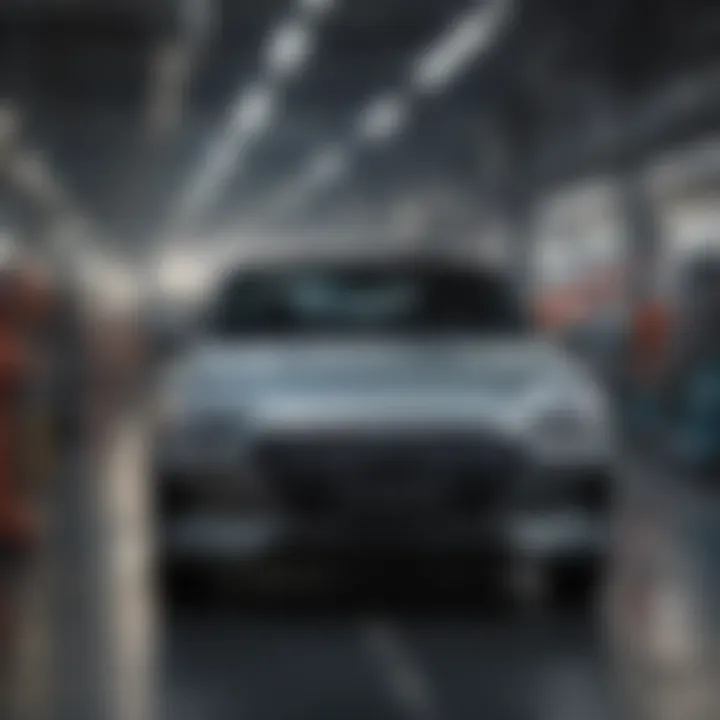
The importance of this comparative analysis lies in several key elements:
- Identifying Competitive Standards: Through this analysis, Hyundai can pinpoint the best practices in maintenance management that lead to reduced downtime and lower costs. By knowing what competitors are doing right, the company can adapt and enhance its own strategies accordingly.
- Evaluating Resource Allocation: An understanding of how competitors allocate resources for maintenance can highlight inefficiencies within Hyundai’s framework. This could reveal opportunities to optimize labor, material costs, and technology investments.
- Adapting to Market Changes: The automotive industry is quite dynamic, with new technologies and methodologies emerging regularly. A comparative look at how other manufacturers manage their maintenance can provide foresight into upcoming trends and how to adapt proactively rather than reactively.
Benchmarking Against Global Standards
A major component of Hyundai's comparative analysis involves benchmarking its maintenance costs against global standards. This means taking a close look at industry leaders not just within the automotive world but also including sectors like aerospace and heavy machinery that deal with similarly complex operational needs.
The process typically involves:
- Data Collection: Gathering data from numerous manufacturers to form a comprehensive view of maintenance cost structures. This can include both quantitative figures and qualitative insights from industry reports.
- Key Performance Indicators: Establishing KPIs relevant to maintenance costs—for example, cost per unit produced, average downtime, and workforce efficiency—all of which help in assessing where Hyundai stands in relation to its peers.
- Best Practices Review: Looking into successful maintenance strategies, like Toyota’s renowned lean manufacturing approach, to see how they minimize waste and enhance productivity.
Through this benchmarking, Hyundai is not just looking to replicate strategies but to innovate within the framework provided by industry leaders.
Lessons from Competitors
Finally, examining the lessons from competitors can illuminate paths that Hyundai might not have considered. Each manufacturer has its unique challenges and opportunities, offering a rich well of knowledge from which to draw.
Some notable insights include:
- Embracing New Technologies: For instance, companies like BMW have heavily invested in predictive maintenance technologies that analyze machinery performance through various sensors and data analytics. Hyundai could adapt similar technologies to its own facilities.
- Workforce Training: Many competitors emphasize continuous workforce training to enhance efficiency. Investing in employee skill development can reduce labor costs and improve maintenance outcomes significantly.
- Sustainability Focus: Companies like Ford are increasingly prioritizing eco-friendly practices in maintenance. By looking at their sustainability initiatives, Hyundai can strive to not only reduce costs but also enhance its market image.
"If you want to have a fulfilling peak performance, learn from those who have been to the summit. Their journey is your map." - Zeno of Citium
In summary, Hyundai's ongoing comparative analysis with other manufacturers is not merely an exercise in observation, but a strategic undertaking that informs and shapes its future in factory maintenance. By paying heed to global standards and gleaning lessons from students of the industry, Hyundai can position itself to not only keep pace with the competition but to steer the industry toward its future goals.
Future Trends in Factory Maintenance
Exploring the future trends in factory maintenance is more than just looking ahead; it's about understanding the evolution of manufacturing landscapes that are shaped by innovation and necessity. As competition intensifies in the automotive sector, particularly for a leading player like Hyundai, focusing on maintenance strategies has become crucial. The aim is not only to enhance cost-efficiency but also to align with global sustainability goals and technological progress. This article unpacks two essential elements of future trends—sustainability in manufacturing and the shift towards smart factories—helping stakeholders grasp their significance.
Sustainability in Manufacturing
Sustainability in manufacturing is not merely a buzzword; it's turning into a fundamental principle that can reshape how companies operate. For Hyundai, adapting sustainable practices means reevaluating their entire life cycle of production and maintenance. This fresh outlook translates into cost reductions, enhanced brand reputation, and long-term viability.
Benefits of Sustainable Practices
- Resource Efficiency: Utilizing fewer resources lessens operational costs and minimizes material waste. Smart usage of materials can enhance the lifespan of the factory equipment.
- Regulatory Compliance: As environmental standards tighten across the globe, staying ahead of regulations can prevent costly fines and promote operational continuity.
- Consumer Appeal: The growing trend among consumers to favor environmentally-conscious brands can drive sales and loyalty.
Beyond logistics, Hyundai's emphasis on sustainability includes integrating clean technologies within their factories. Energy-efficient equipment and carbon-neutral initiatives exemplify specific steps that lead to less environmental impact, while simultaneously reducing maintenance costs over time.
"Investing in sustainable practices today pays dividends tomorrow."
The Shift Towards Smart Factories
The advent of Industry 4.0 introduces a sea change in manufacturing processes, characterized by connectivity, automation, and data-centric management. This shift is not just about having faster machines; it's about embedding intelligence into factory operations, which can similarly impact maintenance strategies.
Key Aspects of Smart Factory Maintenance
- Predictive Maintenance: By employing sensors and IoT technology, Hyundai can monitor machinery in real-time. This anticipatory approach to maintenance helps identify potential failures before they occur, reducing downtime and repair costs.
- Digital Twins: They simulate physical assets in a virtual environment. This enables more informed decision-making, allowing Hyundai to anticipate issues and streamline maintenance efforts.
- Robotic Process Automation (RPA): Automating routine tasks frees up human resources for more complex operations, increasing overall efficiency.
The move towards smart factories encapsulates the idea of optimization—not only in production efficiency but equally in maintenance protocols. Hyundai's readiness to embrace this dynamic environment highlights a strategic foresight that not only addresses immediate challenges but positions the company for sustainable growth.
Closure
The significance of concluding remarks in this article cannot be overstated. As we bring together the various threads of Hyundai's factory maintenance costs, it becomes clear how intertwined these expenses are with broader economic realities and strategic choices. Every element explored throughout this analysis—from the age of equipment to the role of automation—affects not just the bottom line but also the efficiency and sustainability of production processes. Understanding these connections can lead companies like Hyundai to make informed decisions that affect both present performance and future viability.
Summary of Key Insights
From the outset, this exploration has illuminated several pivotal insights:
- Maintenance Cost Components: Hyundai's maintenance costs are influenced by multiple factors including labor expenses, technology integration, and operational strategies. Knowing these components helps in budget planning.
- Preventive vs. Corrective Maintenance: A blend of preventive practices can mitigate the risk of expensive corrective actions. Doing so not only saves costs but also keeps production humming smoothly.
- Technology's Role: The advent of data analytics and automation has revolutionized how maintenance is approached, streamlining operations and reducing downtime significantly.
- Benchmarking: Comparing maintenance costs and strategies with global competitors can provide insights on best practices and opportunities for improvement.
These key points contribute to a robust framework for understanding how Hyundai manages its maintenance expenses and positions itself within the complex tapestry of the automotive industry.
Implications for Hyundai's Future
As we look to what lies ahead, the implications for Hyundai's future are considerable and, in many ways, complex:
- Investment in Technology: Continued investment in advanced technologies such as IoT and machine learning may become non-negotiable. These innovations are not just cost drivers; they're avenues for enhanced predictive maintenance, ultimately leading to greater operational efficiency.
- Sustainability Initiatives: With the growing emphasis on environmental standards, prioritizing sustainable practices in maintenance can positively impact not just cost but corporate reputation and consumer trust.
- Adapting to Market Trends: Global economic shifts often dictate changes in production methods. Hyundai’s agility in adapting maintenance practices will be crucial in navigating these changes successfully.